News & Publications
Lean professionals visit 3sHealth
Dec 28, 2022
Categories: News
3sHealth’s Continuous Improvement (CI) practices recently received a thumbs-up from a group of visiting experts.
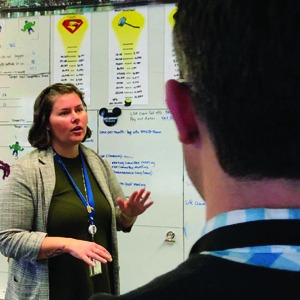
Ahead of attending the recent Lean Practitioners of Saskatchewan (LPAS) conference in Regina, three CI professionals got a first-hand look at some of the ways 3sHealth incorporates CI practices into daily work. Stewart Bellamy, the past president of the LPAS, requested the tour. It included Simon James, who leads the University of Alberta Hospital’s Continuous Improvement division and is the founder of consulting firm Headwaters to Change, and Jim Bennett, the manager of Technology Services for the Greater Saskatoon Catholic Schools. Both are Lean “black belt” recipients with many years of experience in the field.
Simon provided a keynote address at the conference, focusing on using Lean to build an organization’s cultural foundation. He says that was the most impressive aspect of his visit to 3sHealth.
“It’s really easy to show people the artifacts of an improvement journey, that being things that you can visually see and don’t need that much explaining” Simon said. “Right from the very beginning, within three steps, I saw the evidence of a cultural change.”
He noted that evidence that CI methodology has informed the culture of 3sHealth was evident in the pride that employees who participated in the tour showed when discussing their work.
Improvement in action
Physician Consultant Dr. Joy Dobson began the tour with an introduction, with CI Director Jill Forrester outlining 3sHealth’s experiences with continuous improvement since its founding. Benefit Services Director Lorne Shiplack and Manager Sarah Dedman detailed their department’s Daily Visual Management boards and how different teams set up and operate their individual boards.
Simon said those boards and the work teams have put into them are evidence that on-going change and improvement is baked into the culture.
“When we were at each of the boards it wasn’t like it just started yesterday or they didn’t understand it. That board drove activities within the work that they were doing. There was a connection to it, and you could see it, you could feel it, and that’s what it’s about.”
Bellamy, who has previously organized several similar tours, agreed.
“Every time I go, the boards change each time. They’re personalized to the people in the area, and that’s working to keep people engaged and involved. They’re not just going through the motions.”
While Lean practices originated in auto manufacturing and have been widely applied to clinical environments in health care, he feels 3sHealth is a terrific example of how the concepts can transform an administrative environment.
Jill Forrester is always enthusiastic to tell 3sHealth’s story.
“Our corporate processes, such as wall walk, improvement planning, improvement ideas, and visual management, are like a backbone that brings us together and makes us strong,” said Forrester. “To have Lean Practitioners of Saskatchewan come to us again for a tour is always encouraging.”